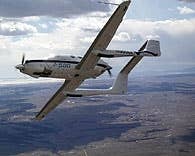
Adam A500 tandem twin
The folks at Adam Aircraft don't particularly like it when their new airplane is referred to as a "push-pull," the most common (and cleanest) name attached to the Cessna Skymaster that made its debut about 40 years ago. The concept of centerline thrust, tandem power, was actually patented by Claudius Dornier in 1937 and developed during World War II.
Maybe "tandem twin" can be made to stick. Whatever, Adam Aircraft has created a twin built mostly of composites that looks back a bit but that is all new and optimizes the concept of the tandem twin, the power available and the current technology.
The airplane pictured and flown is the second Adam A500 built by the company. (Scaled Composites built an initial proof-of-concept airplane that looked similar but really wasn't.) The first Adam-built airplane has been retired to static test, and flight testing is continuing with this second airplane. A third airplane is now being built and may have flown by the time you read this. The third airplane will be the first to fully conform to production standards.
A lot of people have seen the Adam A500 at airshows, in a crowd. The airplane has a different personality when you see it alone, in a hangar or on a ramp. Everyone agrees that it looks bigger. It is. With a 44-foot span, 36.7 foot overall length and 9.5 foot height, it compares dimensionally with a Cessna 421 and is substantially larger than the four-seat Cessna Skymaster. The size is enhanced by the fact that it has more pieces than a conventional airplane. The booms are large and gracefully shaped as they arch up to the horizontal tail, which is high above the power pulses from the props. The tail is quite shapely and couldn't have been as nice had the airplane been made of metal.
The wings are nicely shaped, too, and have removable leading edges for access to control cables and TKS deicing components. The horizontal tail also has a removable leading edge. The TKS system was recently chosen as the ice protection for the airplane after Adam considered deice boots and other ice protection technology.
It apparently made more sense for the control surfaces to be metal, so they are. Different things affect designs in different ways because in transport airplanes a first move to composites has been in control surfaces.
The airplane I flew had a removable door with no hinges and no steps. It was not pressurized and may never be. It did not have nosewheel steering as the production airplane will have. Nor did it have cabin heating or much of an interior. The two seats installed, in the cockpit, were fixed, not adjustable. The airplane was being operated as an experimental, approved by the FAA for market survey work but restricted to day VFR conditions.
The two A500s have flown more than 200 hours, but there is much flight testing left to be done, and the FAA will want data from testing with the fully conforming third airplane. The airspeed envelope had been examined out to 180 knots indicated airspeed, which is well within the green arc on this particular airplane. Airspeed limits will be established in the final testing phase.
Boarding the Adam A500 is currently done with one of those three-step ladders, just like the one that I carry around so I can look in the gas tanks and that my wife likes to use boarding our P210. The production airplane will have an airstair door. The door opening is large and the cabin is entered just aft of the cockpit. With no seats, the cabin looks huge and promises to offer luxurious seating for four in a club arrangement.
The flight deck is spacious and, because the fuselage is wide, elderly or portly pilots won't get a cramp in the old tummy trying to wedge in there.
The instrument panel is conventional. The circuit breaker panel is to the left, and many breakers on this airplane are banded because of equipment that isn't installed or operational, such as ice protection and an autopilot.
The instrumentation is conventional. Adam plans to evolve to a glass cockpit, but for now the concentration is on certifying the basic airplane.
The power controls appear to be low on the panel compared with other twins, but the controls come naturally to hand, so the location is fine. The left controls are for the front engine, the right for the rear.
The panel is a little farther forward than most. Somehow a panel farther away is easier to scan than one that is right in your face. This one seems especially spacious because of the generous width of the airplane.
The panel's most wonderful feature, though, is that there is no control wheel jutting out of it, taking space and obstructing the pilot's view of the panel. The Adam A500 is flown with a sidestick, which is being embraced in most of the new-design airplanes and which is a great way to fly.
The Adam is an all-electric airplane with two buses and two batteries. Excellent work has been done in this area, both by the FAA and the manufacturers, and those short-lived old vacuum pumps are just not going to be found on a lot of new-design airplanes.
For engine instrumentation, the A500 has a Vision Microsystems VM 100 engine management system. This was, to me, not a great step forward. The old Cracker Jack box mechanical instruments are easier to interpret, but then I'm used to them and not to the Vision system.
The airplane also has a Vision electronic checklist and caution advisory system that seems to cover everything.
Glenn Maben, one of the best demo pilots I have flown with, briefed me on the airspeeds to be used and offered one bit of advice about the sidestick. When the ailerons are neutral the stick is maybe 20 degrees to the right of being straight up and down. Apparently some pilots have wanted it straight up and down and have thus found the airplane rolling to the left at liftoff.
On Cessna Skymasters we used to always start the rear engine first. On the Adam they have been starting the front Continental TSIO-550E first. Full authority digital engine control (FADEC) will be available on the airplane but is not fitted on this particular airplane. That will eliminate the mixture control and automate the operation of the engines.
The starting is like any injected Continental, and even with the front engine running it is plain that the rear engine is coming on line just fine.
The visibility is great, and taxiing with the non-steerable nosewheel is no problem. Certainly if the production airplane had the steering of this one it wouldn't be a problem.
I look at a lot of things on a new design to try to form an opinion of what that first takeoff will be like. The location of the A500 main landing gear suggested to me that the liftoff would be just right. If the landing gear is located a bit aft of where it really should be, the forces required to unstick are often high, meaning there will be a tendency to over-rotate, which often results in a little pilot-induced pitch oscillation after takeoff.
The Adam sits on the ground at a neutral angle of attack. This is also ideal for takeoff because the airplane neither gets light on the wheels in the roll nor requires a big tug for liftoff.
Finally, when the Adam is viewed from behind you can't see much of the prop blades. This often means that the static thrust isn't going to be too whippy.
The airplane had 120 gallons of fuel on board (total capacity is 270 gallons) and two standard people, so it was what you would call "light." Remember, too, as I relay thoughts about the A500, that the airplane flown was of a design that has flown only a couple of hundred hours and that is in a state that is subject to change and constant refinement.
My advance thoughts about the takeoff were right and they were wrong. The wrong part relates to the static thrust. It felt very good as the 700 horses were allowed to gallop down the runway. The sense of acceleration felt much like that found in a conventional twin. Maybe good propeller work by Hartzell helps on that static thrust.
The transition from the roll to flight was neat, too. It's a challenge to think about how to do it just right and a reward when the airplane agrees with the way it is done. Vr was 85 knots and the speed was up to about 95 when the rear wheels broke the surly bonds.
Because we were operating under the Atlanta Class B airspace (from Dekalb-Peachtree, PDK), the initial climbing was done at cruise climb. The indicated airspeed was 140 knots and the rate of climb probably averaged 800 to 1,000 feet per minute in the roiling air of an enthusiastic spring day.
I will give a report on my impressions of the sidestick when the flight is completed.
Once the last ring of the TCA had passed above, as shown on the two Garmin GNS 530s that will be standard, Glenn advanced the power to full and we went for the best rate of climb airspeed where the vertical speed vaulted up to 2,000 feet per minute. The airplane is going to be a strong climber.
After a little of that we were passing through 10,000 feet. Glenn reduced power on one engine to zero thrust, and by the time everything settled down we were at 12,000 feet and climbing at about 500 feet per minute. The airplane is going to remain a strong climber even with but one engine running.
The need for speed determines how much money we spend on airplanes, and the A500 does well in this regard. An upwind/downwind GPS run at 10,500 feet verified that production airplanes should cruise at least 200 knots at that altitude while burning 40 gallons per hour total. This airplane didn't have main wheel well doors, which I understand will be fitted; it had a test boom, it had that temporary door that probably added some drag, and it lacked the final aerodynamic tweaking that is always good for a few knots.
Given the likely specific fuel consumption of the engines, 40 gallons per hour is about 75 percent power. So, lets say the conforming airplane will do 205 at 10,500 feet. Using the speed increase with altitude that is found in most other turbocharged twins, that would equate to a cruise of about 235 knots at FL 250, which will be the airplane's maximum certified ceiling. If the temperature aloft is warm, though, the engines probably wouldn't make 75 percent power at 250. In standard temperature, the engines are said to be able to maintain full 350 horsepower to 17,500 feet. The cabin will be at 8,000 feet at FL 250.
On descent I pulled the power back enough to stay comfortably below that 180 knots to which they have tested and to get a healthy rate of descent that brought the power to well below 20 inches.
At higher speeds the airplane rode well in the bumps. In fact, from what I saw, the airplane really does give a good ride in turbulence at any speed.
As we got close to PDK, the tower asked if we could land on Runway 27. Glenn said we could, though it appeared that we were a little close and high. I slowed to 140 knots, the speed they are using in test for the landing gear extension, and Glenn extended the gear and takeoff flaps. The airplane started coming down well and with just a little widening of the pattern we were able to turn final with the visual approach slope indicator saying "yes."
Glenn said to use 105 as a Vref with full flaps and we did. As the end of the runway was approached, I reduced the power to idle, the airplane floated just a bit and then touched down. The trailing-link landing gear helps the pilot's ego on landing.
Glenn then informed me that I had set a record by landing the A500 on the shortest runway, 3,378 feet, that it had ever used. With enthusiastic use of the brakes we could have turned off 2,250 feet down the runway. There was about a 10-knot headwind component on the runway and for a serious short field the Vref could be reduced to about 95 knots, which is still more than 1.3 Vso.
I thought the sidestick in the airplane is great. In roll, especially at higher speeds, the stick forces are on the high side but no higher than in my P210, for example. In pitch, everything seems just right. There are no big changes when the configuration of the airplane is altered and the coolie hat for the electric trim is at your thumb. Glenn asked what I thought of the speed at which the trim moves. It was a little fast for me, but the speed at which the trim runs will be determined during S-Tec autopilot certification, which should be under way as you read this.
The only thing I would look at on the sidestick is the relationship between the grip and the armrest. On this airplane my arm was not level on the rest when I gripped the stick. This meant that some of the roll commands were with arm as opposed to wrist motion. That did give more leverage but it also meant that roll commands were not as smooth as they should have been.
Because this airplane isn't "finished," I couldn't make a guess on how the sound level will be, but I will say that the cabin was quieter than I thought it would be. My expectations were low, though, because sharing a composite tube with two engines can be like relaxing inside a drum. There was some low-order vibration that usually comes when the engine moves in the cowling under power and touches something.
The A500 was in Atlanta for, among other things, a showing to owners at AirShares Elite, a fractional provider that currently operates 14 Cirrus airplanes.
AirShares finds a great deal of A500 interest among its Cirrus shareholders and has ordered three of the airplanes. The deal is $170,000 for an eighth share, $1,600 a month for management and $160 for each hour flown. David Lee of AirShares reported six verbal commitments for A500 shares after the airplane was shown in Atlanta. He also reported that the insurance weenies were mentioning an instrument rating. One thousand hours total time with 100 multiengine, factory training and 25 hours in type are the requirements to fly the airplane solo.
The 100 hours multiengine requirement seems beside the point. There is simply no similarity between the technique required to handle a twin with wing-mounted engines after one fails and that required to handle a tandem twin after an engine failure. With the tandem you fly exactly as you would in a single with no power. Maintain the proper airspeed and follow the proper procedures and things work as well as possible. No fancy footwork required.
The Adam A500 isn't a revolutionary airplane, but what it does is give the advantage of tandem power with no performance penalty and no flying qualities penalty, as was found in the Cessna Skymaster. Any pilot who is competent in a high-performance single will be perfectly suited to fly the A500 with the extra safety potential of a second engine. In fact, when you compare the A500 numbers with those of the Cessna 421, everything is close without the potential flying challenge of dealing with the asymmetric thrust if an engine fails.
Adam projects certification by this summer, but that looks ambitious to me. There are too many battles yet to be fought. And the elements that affect every new design-primarily weight and cost-have to be addressed every step of the way. Adam does appear up to the task, though, and I'm looking forward to a nice long trip in an A500 and to hearing them on the frequency and seeing them on the ramp. It's a great and unique new shape in the sky.
2003 Adam Aircraft A500 |
The airplane flown for this report did not conform to production standards. The production airplanes will have, as standard equipment, two Garmin GNS 530s, a Garmin transponder and audio panel and an S-Tec 55X autopilot. Deicing, air conditioning, radar, and full authority digital engine control systems will be extra. The price reflected here is with all options because that's how everyone will order the airplane. The performance and weight numbers are preliminary and from Adam Aircraft. If you want more information about the company, the airplane and the testing and certification process, Adam has an excellent website: www.adamaircraft.com. |
Price fully equipped..............................................$1,019,000 Engines Continental....................................TSIO-550, 350 hp TBO.........................................................1,600 hrs/12 years Propellers....................................................Hartzell, 3-blade Length......................................................................36.7 ft Height........................................................................9.5 ft Wingspan..................................................................44.0 ft Maximum takeoff weight..........................................6,300 lbs Empty weight..........................................................4,200 lbs Useful load............................................................2,100 lbs Usable fuel...............................................230 gals/1,350 lbs Full fuel payload........................................................750 lbs Maximum rate of climb, sea level............................1,800 fpm Single engine rate of climb, sea level.........................400 fpm Maximum certified operating altitude.........................25,000 ft Cabin altitude at 25,000 ft.........................................8,000 ft Max cruise, at 22,000 ft.............................................250 kts Stalling speed, flaps down............................................70 kts |
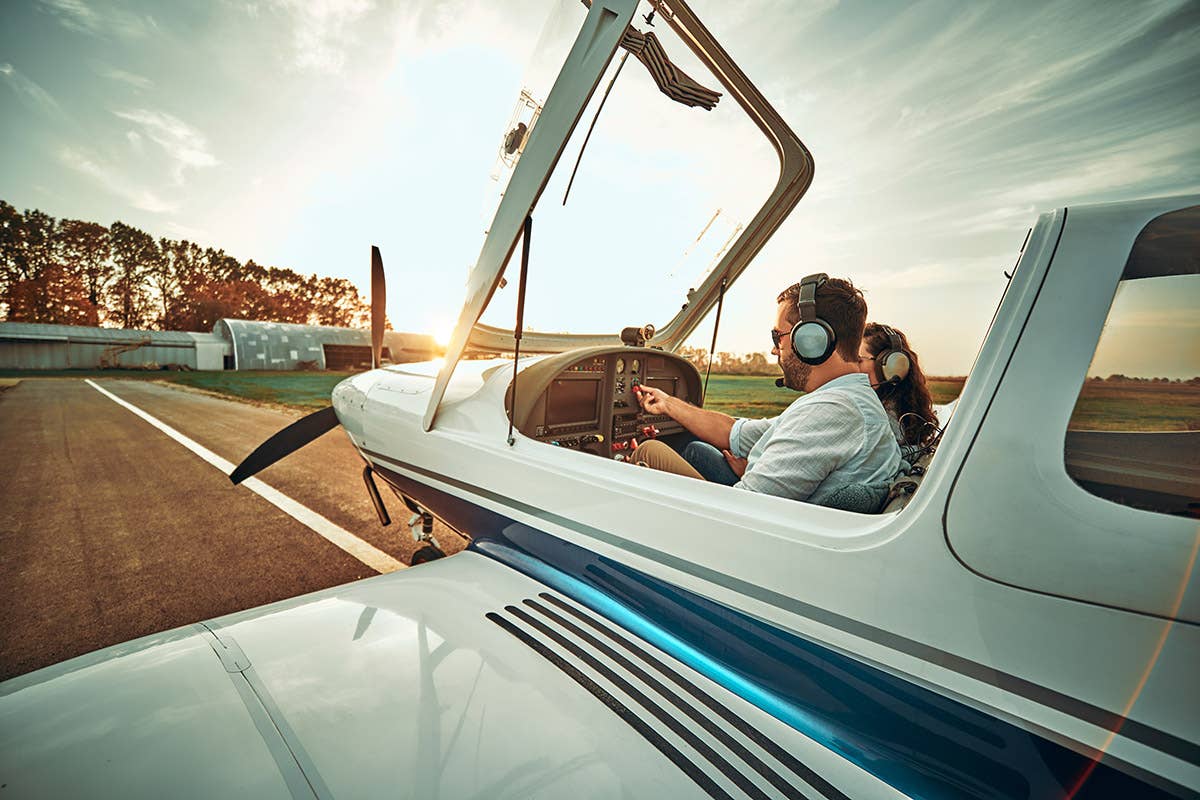
Subscribe to Our Newsletter
Get the latest FLYING stories delivered directly to your inbox